In recent years, energy conservation has become a hot topic in new automotive technologies and trends. Looking back over the past 20 years, the electronics of automobiles have been driven by drivers for more comfortable and luxurious equipment such as electric windows, electric sunroofs and convertible covers, advanced audio equipment, electric seats, air conditioning or electro-hydraulic power steering systems. Driven by the thirst, these devices all add to the demand for semiconductors and electronic components. Now, the primary goal of electronic car design has changed. While luxury equipment and better driving functions are still important for the car, most of the electronic systems used in contemporary cars are now to reduce emissions, improve fuel efficiency, and reduce power consumption in in-vehicle systems. For the driving force.
The best way to achieve this goal is to replace the mechanical and hydraulic systems of the car with more efficient and intelligent electronic systems. Typical examples are electric hydraulic systems that replace hydraulic or electro-hydraulic systems; electric motor drives replace continuous-running belt drive systems like air conditioner compressors, turbo chargers, or other pumps and fans. Even some lighting applications, such as energy-efficient "high-intensity discharge lamps" (HID) or LED lamps, are used to replace traditional bulbs that lack efficiency. Ultimately, the internal combustion engine will also be replaced by an efficient electric motor, as we have seen in the powertrains of hybrid and electric vehicles.
Automotive electronics also enables International Semiconductor Corporation (IR) semiconductor suppliers to develop high-efficiency power management solutions to maximize the energy efficiency of these applications. IR's advanced power management solutions combine state-of-the-art silicon technology with revolutionary new packaging technologies to simultaneously improve the performance and durability of automotive systems. Especially in terms of packaging, we bring innovative solutions to system designers and new ways to design ECUs, motor drives and power supplies.
Today's silicon technology enables very good switching, such as the latest channel MOSFETs and IGBTs. However, related packaging techniques often use a very conservative soldering method to attach a silicon chip to a substrate or lead frame and bond the surface with bonding wires. As early as 2002, IR has begun to develop a new connection interface, hoping to connect our best silicon technology to power circuits with a simple package, and to minimize the interface between current and heat flow. The end result is that we have developed DirectFET technology that eliminates bond wires. The implementation of this technology relies on the front metal of the silicon switch being solderable so that MOSFETs surrounded by a simple metal case can be soldered directly to the printed circuit board. The concepts presented in Figures 1 and 2 are primarily simple in design, minimizing material and interface, and most particularly eliminating the need for bond wires to achieve the best power and temperature performance. In addition, this concept can also improve the quality and reliability of automotive systems because it eliminates the dominant failure mode in the vehicle's power cycle: the so-called bond wire detachment.
This article refers to the address: http://
Figure 1: DirectFET soldered to the PCB.
Figure 2: Cross-section of the DirectFET: The silicon chip's temperature and power interface are shrunk as much as possible, while power and temperature performance far exceeds the standard package with bond wires.
The direct packaging concept is ideal for automotive applications that require superior performance, quality, durability and long-term reliability. At the same time, IR optimized the DirectFET concept, which resulted in the DirectFET2 product line that we introduced at the beginning of this year and is fully car-recognized. The car chip is surrounded by a small enclosure, allowing customers to introduce very innovative design concepts for their electronic control units and power stages. These DirectFET2 switches can be dissipated by different methods, including heat dissipation from the top of the device, eliminating the need for components to pass through the PCB, or even the need for cooling on both sides of the ECU housing, or reducing the temperature by other heat sinks in the ECU design. . Customers can therefore produce proprietary system solutions that stand out from the competition with other standard package parts and bond wires.
Figure 3: Various innovative cooling methods for DirectFET2 for automotive use
IR extends its bondless line strategy to all automotive power switches. Its latest generation of IGBTs also feature IR's proprietary front metal solderability technology, which provides a chip connection with no bond wires at all, and a two-sided heat dissipation concept for high voltage systems using IGBTs and diodes. As far as I know, IR is the first company to introduce commercial vehicle-accepted IGBTs with bare chips and front metal solderable technology, enabling customers with silicon processing capabilities to build and design their own double-sided heat-dissipating no-bond power modules. Or power level. With IR's front metal solderable devices, system designers who often don't have access to proprietary silicon technology can now enjoy the world of "wireless car power management."
In addition to bare chips, IR will also offer a proprietary chip carrier solution. The solution comes with front metal solderable IGBTs to support customers who are incapable of handling bare chips. The most advanced high-performance IGBTs are fabricated on very thin wafers and are only 60 to 70 microns thick. These silicon wafers are both thin and flexible, just like paper, so they must be processed using extremely specialized procedures and expensive equipment. Many first- and second-tier system suppliers are reluctant to invest in such expensive equipment, and do not want to experience the slender chip processing that requires long-term learning, and do not want to withstand the very high-end processing during thin chip processing. Rate loss.
The new car power switch from IR, which is attached to a proprietary chip carrier, will wipe out the above concerns. We will provide a standardized proprietary chip carrier with pre-attached IR large chips (IGBTs and MOSFETs). They will then become part of the customer's power module. For example, our DirectFET2 metal case becomes part of the PCB circuit and allows everyone to utilize the most sophisticated IGBTs and thin chips instead of thin chip devices. As a silicon technology expert, IR will be responsible for the most difficult part, that is, the manufacturing process of thin chips into substrates, and the final test of switches at the bare chip and wafer level will be solved one by one. As long as you use IR's automotive front metal weldable product line, even standard mounting machinery and welding equipment will be sufficient to handle very advanced power modules or ECU concepts.
For our customers and system designers, the biggest benefit of the new device is not just improved power performance, better switching performance, optimized double-sided cooling (we can increase the overall heat exchange area by at least 50%) A 35% reduction in RthJC and a 25% increase in silicon current density), as well as a simple manufacturing process, are important advantages. Another extraordinary benefit will be realized in terms of system layout and application size associated with the application, as well as on the life expectancy of the vehicle. When the bond wire breaks away in the relatively durable DBC module or the first failure mode in power cycle pressure, the bondless IGBT with IR proprietary front metal solderable technology will have the opportunity to extend the power cycle capability by an order of magnitude. .
Figure 4 shows the power cycle test that the IR is running. This test pin is for a customer's custom IGBT system, which will break the bond wire that occurs after several 10,000 temperature cycles and compare it with the results of the same continuous cycle test using the no bond wire system. You can see the result. Shows great difference. Power cycle energy efficiency system designers can reduce their power stage size with significant reliability extensions.
Figure 4: Power cycle energy efficiency comparison of bond wire IGBTs and bondless wire double-sided solder IGBTs in proprietary customer ceramic packages. The two graphs above show different temperature and pressure conditions, and each ribbon represents each individual device in the test.
In order to avoid premature bond wire breakout failures in practical applications, designers often use expensive substrate and heat sink methods, plus oversized power switches to reduce the Delta-T temperature swing for each power cycle. . In comparison, the chip size of a bondless line system can be significantly reduced, while the system can operate longer under more severe cycle conditions. This shows that inverters, DC-DC converters and other power management applications in automobiles can significantly reduce system cost through front metal solderable devices. Designers can therefore improve on performance, reliability and more.
To help system designers complete the entire power stage development with the right control IC, IR offers a variety of automotive driver IC options to meet advanced inverters, converters, power supply topologies and system requirements. Our proprietary automotive high/low voltage gate drivers offer exceptional durability and latch-up immunity. In the voltage range below 75V, the design can operate the driver based on a proprietary intelligent power program, enabling very large current switching. When the voltage is between 100V and 1,200V, IR also offers a family of very high voltage interface isolated driver ICs with a market leading negative transient voltage spike safe operating area (NTSOA). The failure mode of the IC is usually caused by a large current inductive load to realize the switching half bridge, thus causing a large negative voltage spike, which is called a latch-up effect. Designed for durability and latch-up immunity, these ICs are the best choice for driving large IGBTs with very high current densities, such as front metal solderable devices. If the system designer needs more drive current, the buffer IC provided by the device can also be used to provide a maximum current of 10A.
In summary, IR offers a range of devices that enable automotive power system designers to choose the complete chipset for very advanced "wireless" power management to support the energy efficiency of future vehicles, even in the most demanding environments. With difficult switching tasks, these devices can handle them as well.
With spiralling energy costs accompanying the constant need to replace bulbs and tubes our 2 ranges of Marine Aquarium Lighting makes perfect sense.A conservative savings in electricity consumption of up to 50% can be achieved over metal halides and 25% onT5 Fluorescents.
2 Manual dimmers for White, Blue change the intensity of lighting
Simulates the sunset and sunrise
55pcs 3w leds offer lighting to tank effectively
Adjustable kits, detachable cords
Philizon Lighting is dedicated to provide high quality and durable lighting product for customer with very competitive price.Our products mainly foucs on Led Grow Lights and LED Aquarium Light .The equipment and materials to produce Hydroponics Led Grow Light and marine Aquarium Led Light fixture imported from Taiwan, Japan, Korea and Unites States, such as automatic SMT machine, reflowsoldering machine,all kinds of electric test equipment, large integrating sphere and such sorts of productionand R&D equipment.
Item Display
Key Features
1.The lifespan is over 50000 hours,low maintenance costs.
2.Energy conservation,saving over 80% energy than the traditional HPS.
3.High light efficiency,90% of the light will be absorbed by the aquatic plants,while just 8%-10% to the HPS.
4.Build-in cooling system,could solve the heat dissipation excellently.
5.Built-in power supply, CE approved, No setup required, just simpler and safer plugs directly into AC85V-264V, no reflector & ballast needed.
Package Include
1 X Led Aquarium Light
1 X Free Hanging Kit
1X Free Power Cord
All the lamps have passed strict quality examination and are packed carefully before shipping.In order that our customers get high quality lamps,we attach importance to every details.
Application
1. coral reef lighting,fish tank lighting,coral reef tank lighting
2. Aquarium Lighting ,aquarium art,aquarium shop,aquarim centre
3. fish bowl lighting,fish lighting,freshwater lighting,saltwater lighting
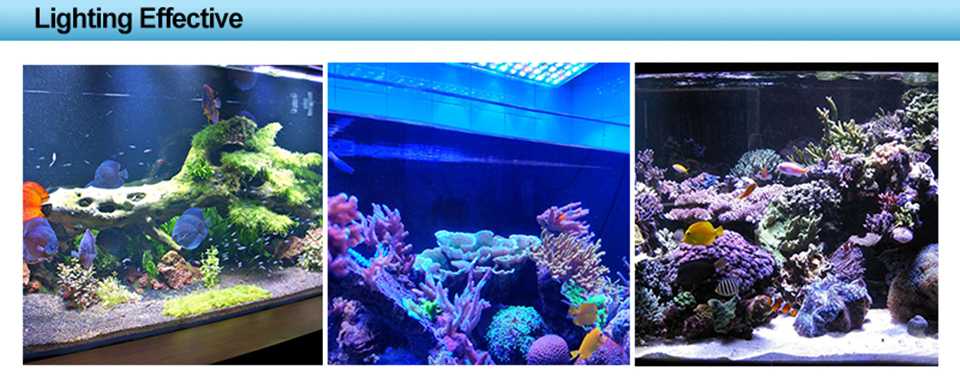
Our Led Plant Grow Light and led aquarium lamp are popular in led market,cause its elegant outlook and its high quality and competitive price.We are eager to kick off cooperation with you, our valuable customers. Let`s work together and save the energy.
Warmly welcome to visit Philizon in Shenzhen China.
Marine Aquarium Lighting
Marine Aquarium Lighting,Marine Led Aquarium Lighting,Marine Led Lighting,Marine Aquarium Led Lighting
Shenzhen Phlizon Technology Co.,Ltd. , http://www.philizon.com