Electronic equipment manufacturers often use electromagnetic interference (EMI) and radio frequency interference (RFI) shielding to protect sensitive digital circuits from external radiation while also limiting the potentially harmful radiation emitted by their products. But these manufacturers face the daunting challenge of meeting EMI/RFI shielding requirements, such as material selection and the conversion of selected materials into effective shielding components. To address these challenges, many OEMs turn to companies that specialize in flexible materials conversion.
This article refers to the address: http://
In the early stages of the project, top companies can provide critical engineering support to improve product design and manufacturability. Leading converters also have automated equipment and highly trained professionals to perform the various conversion tasks required in this industry.
Basic principle of shielding
EMI/RFI shielding is a function of many consumer electronics products such as televisions, radios, cell phones, and computers, as well as devices used in medical and aerospace applications. The shielding function of these devices is achieved through the Faraday cage. These Faraday cages cover all electronic components and are effective against electromagnetic radiation.
Faraday boxes are made from many flexible materials. Companies such as 3M, Parker Chomerics, Laird Technologies, Saint-Gobain, Permacel and Intertape Polymer Group are manufacturers of these flexible materials (see photo).
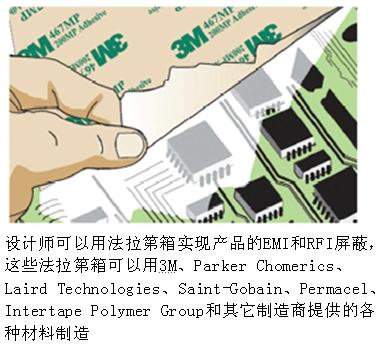
Common EMI/RFI materials are: (1) Metal foil tape: relatively easy to manufacture. The use of tape with aluminum foil and copper foil backing provides excellent shielding without the need for expensive metal plating of the outer casing. (2) Metal-filled rubber: These materials are suitable for shielding applications requiring gap filling and shock absorption. (3) Wire mesh: mainly used for EMI gaskets. The wire mesh material has a better heat dissipation effect than the metal foil, but it is heavier and takes up more space.
Help from the converter
Converters need a comprehensive screening of flexible shielding materials from leading suppliers. At the beginning of the project, the converter's engineering team helped the OEM to select the material that best fits the particular shielding application. The converter's selection of materials is based on reference data provided by the material supplier and their extensive experience in shielding applications.
To understand the potential value of this basis, consider the case where OEMs designate copper EMI/RFI materials as shielding strategies. Copper has excellent shielding properties and is heavy enough to withstand soldering when connecting wires. But copper is more expensive. In this case, the converter may think that the foil tape, which is much cheaper than copper, can also be successful.
In other cases, the converter's engineering team may recommend simultaneous testing of shielding options with greater robustness and lower robustness. If the test indicates that the application's shielding requirements are met, then the user can choose a less robust (and less expensive) option.
Based on user requirements, the converter can arrange for EMI/RFI testing services with the material supplier. Sometimes this test may indicate that the user's original design does not provide adequate shielding. When this happens, the converter's engineers may recommend the use of foil tape to enhance the shielding performance.
Other design services
Using renowned 2D and 3D solid-state modeling software, conversion engineers can use OEM electronic designs directly or generate their own drawings. These capabilities allow converters to help users turn concepts into real products, easily point out problems, and suggest blocking configurations.
Sometimes, designs made by OEMs with little or no shielding experience can be difficult and/or expensive to use in batch manufacturing due to excessively tight tolerances, unrealistic configurations, and the like. Leading converters can quickly identify such problems with their engineering resources and manufacturing expertise, and provide other manufacturing strategies that still meet OEM shielding requirements.
Another key is to quickly launch a sample of the shield design and quickly prototype the shield design and it is free to the user. This service helps OEMs develop better shielding solutions and provides their conversion partners with the opportunity to test manufacturing processes that are required to support full-load production.
Conversion company engineers can provide samples for testing and evaluation using user samples, manual sketches or complete engineering drawings. With advanced equipment such as lasers, water jets and Zund platform prototypes, a small number of prototypes can be produced in less than 48 hours without processing.
Many prototype production processes require multiple iterations to produce a final design that meets all requirements. Throughout the process, the converter's engineers will help OEMs adjust the design to directly meet form, assembly and functional requirements.
Turn design into product
Once the design is complete, the converter will buy the necessary materials and turn them into shielded products. The general conversion process produces elongated metal foil tape rolls and die cutting components of various shapes. In addition, some converters have advanced production machines, such as lasers and water jets, that cut complex designs into a variety of materials.
The converter can also laminate multiple materials together to form the final product. Some leading companies are equipped with machines of various widths that enable the lamination of different materials with different adhesives. Lamination capabilities range from single-step processes to multi-material operations with integrated final processes such as punching and cutting. Some converters can laminate up to five different materials at a time. Laminate products include a material for EMI/RFI shielding and another material that provides electrical insulation or other necessary characteristics.
Some applications may require tight tolerance die cut parts and complex shield configurations, such as a composite containing an insulator like Mylar, on which a die cut shield "island" is placed. Or a multi-layer product consisting of metal foil, adhesive and special liners that can be easily removed by the OEM's pick-place machine during the final assembly process. The converter can laminate the three units together and then die-cut the laminate to produce a finished product.
When a shielding application requires a box-like part, the converter can provide the user with a creased or folded material so that the OEM can easily fold the planar material along the crease or fold line to form the desired shape.
Leading converters also offer printing capabilities that can handle everything from basic monochrome applications to complex color designs. They can use both water and UV-curable inks to perform printing on a variety of shielding materials.
Summary of this article
Companies specializing in flexible material conversion can help you make it easier to shield sensitive components from EMI and RFI. Leading converters have in-house engineering resources to help electronics manufacturers select the best materials and designs for shielding applications.
After buying raw materials from many leading suppliers, converters can turn them into shielded products using a variety of manufacturing processes. In many cases, converters can use a variety of materials and technologies to create effective solutions to the most stringent shielding problems facing a wide range of industries.
LED Headphones are a time-honored product. It is not a simple headphone, in the strict sense. It is not just a headset that provides a high-quality audio experience, but also a trendy, fun, life-giving and enthusiastic product. The introduction of the LED Headphone will bring fresh blood to the entire headphone market. It is a cross-border digital headphone.
Advantages:
1: Bright colors, dazzling in the night, fashion avant-garde.
2:180° angle illumination. 3.The color of the light is even and delicate, bright and rich.
LED Headphones
LED Headphone,LED Bluetooth Headphones,LED Light Up Headphones,Wireless LED Headphones
Shenzhen Linx Technology Co., Ltd. , https://www.linxheadphone.com