In recent years, automakers have been working hard to gain the favor of consumers, but with the participation of emerging market automakers, competition has become increasingly fierce. These emerging car manufacturers have abandoned traditional solutions, benefiting from new tools and processes. This new design approach shortens the cycle from design to launch, and improves product quality and product competitiveness.
This article refers to the address: http://
When a new generation of consumers buy cars, they are not only better than the past, they are more eager to have more choices. Automakers need to make significant changes in the process flow and the functional organization within the enterprise to respond to such new spending habits. On the one hand, consumers want their vehicles to be more personalized through different configurations, and on the other hand, they hope to get these options without increasing the price. However, automakers hope to capture the market more effectively through “global modelsâ€, while satisfying consumers' willingness to choose, but also meeting different regulatory requirements and vehicle changes.
The diversity of vehicle configurations requires not only the cooperation of the design and manufacturing departments, but also the after-sales maintenance department to provide appropriate maintenance and repair data for each vehicle. The proliferation of automotive configuration complexity and the resulting cost issues associated with production scale, end-of-life, certification, documentation, etc. are now testing automakers. How to resolve the contradiction between the value of diversity and the cost of complexity has become one of the biggest challenges facing automakers today. This is most felt in the field of electrical design because “electrical systems†are influenced almost by all design decisions and customer choices: for example, different configurations may have hundreds of millions of different permutations.
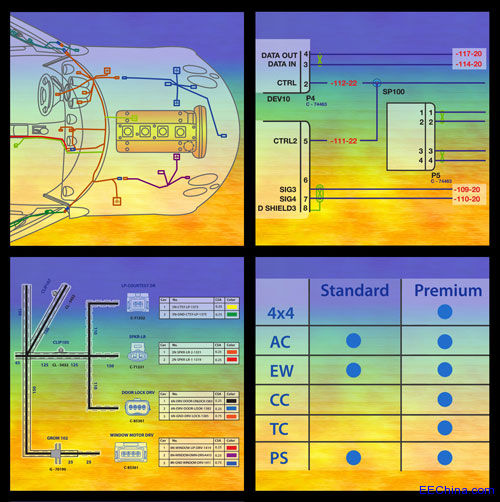
In electronic/electrical system design, the process of transforming from demand to product is quite complex and central to the entire system engineering. First, the requirements are analyzed and described as features, and then the features are broken down into functional modules. The functional modules together form a logic system that is connected to each other through thousands of analog or digital signals. The logic system is placed in the car in physical form, and its signals and equipment are tagged with options and vehicle models to reflect the product plan (description of features and models - varies by region). The integrated design is then carried out by a wide range of supply chain vendors before final integration and certification by the manufacturer (OEM). In addition, design change management in this process has always been a problem. Finally, repairs and warranties related to the brand image must also provide appropriate data for each specific vehicle (through legislation). easy to say, hard to do!
It is clear that the past has used a mix of internal solutions and a variety of commercial software to meet the needs of the automotive industry. How to solve this contradiction has become a hot topic in the automotive industry, and because of this, a solution that meets the requirements of electronic/electrical complexity has become increasingly clear. First, the transition from a file-based design process to a data-based and cross-domain integration design process is imperative. This shift allows the design to be done in a higher-order abstraction layer. After importing the corresponding design model and design constraints from different aspects, the electrical design of the car will be automated in an integrated manner. It also enables the continuous improvement of the company's self-designed intellectual property (IP) into the core of the solution. This shift shortens the product design cycle and provides a viable way for designers to evaluate multiple designs in terms of configuration complexity. In addition, modern IT solutions such as Service Oriented Architecture (SOA) and Lifecycle Collaboration Open Service (OSLC) provide a data platform that is easier to share and view (all platform-wide sharing, not just a single area of ​​data creation) .
Fortunately, commercial software that meets these requirements is emerging to support the modern electronic/electrical design process. For mature automakers, the ability to adopt these new technologies and gain a technological edge over their proven cost advantages will be the key to surpassing emerging competitors.
No Hand Washing Soybean Milk Machine
White Color Soy Milk Maker,No Hand Washing Soybean Milk Machine,No-Wash Smart Soymilk Maker,Automatic Soymilk Maker
JOYOUNG COMPANY LIMITED , https://www.globaljoyoung.com